The future of manufacturing
Industry 4.0 promises transformative changes in manufacturing, bridging the gap between traditional processes and futuristic innovations.
As technological advancements and huge investments are key success factors for decision makers, the debate between micro-factories and macro-factories becomes relevant.
Micro-factories, in particular, exemplify this evolution, offering more efficient, digitized, and localized production.
Here’s a closer look at why micro-factories matter and how they compare to their larger counterparts. It stresses the focus on the role of digitalization and AI in optimizing manufacturing processes.
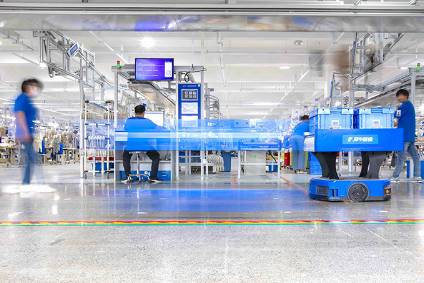
Some reasons Micro-factories matter:
1. Cost Savings. Micro-factories reduce investment needs by focusing on specific cells or components. This modular approach eases maintenance, standardizes operations, and lowers capital expenditure. Businesses scale operations more flexibly and cost-effectively. This is particularly beneficial for small and medium-sized enterprises (SMEs).
2. Personalization. Micro-factories excel in producing highly personalized products and services quickly and efficiently. Agile and automated systems enable quick adaptation to market demands, offering tailored solutions. This capability is crucial in industries where customization is a key differentiator, i.e. fashion, electronics, and automotive spaces.
3. Resource Efficiency. Consuming less power and resources, micro-factories are inherently more sustainable. By localizing production, they shorten transportation distances, reducing associated emissions and costs. This efficiency supports just-in-time manufacturing, minimizes waste, and aligns with environmental sustainability goals.
4. Local Impact. Micro-factories support localized manufacturing, which aligns with consumer preferences for authentic and locally produced goods. This approach stabilizes prices amidst global disruptions and create local jobs. And it addresses automation-related upskill for employees. By fostering local economies and supporting circular economy, micro-factories drive sustainable growth and community resilience.
Case Study: Fieldmade
The Norwegian Fieldmade exemplifies the micro-factory model. This is a clear case of deployable additive manufacturing and digital supply chains. They have developed mobile micro-factories for on-demand spare part production.
By digitizing these factories, they have enhanced environmental control, process stability. They have embedded predictive maintenance and remote assistance, deploying viability and efficiency of micro-factories.
Centralized Macro-factories: the scale advantage
1. Economies of Scale. Macro-factories benefit from economies of scale, producing goods at a lower per-unit cost due to large-scale operations. This cost efficiency is vital for industries where price competitiveness is essential, such as consumer electronics and automotive manufacturing.
2. Advanced Automation. Extensive automation and advanced manufacturing technologies in macro-factories lead to higher efficiency and production consistency. The huge investments in automation are feasible in larger operations, where the return on investment is significant, even if on longer periods.
3. Global Supply Chain integration. Macro-factories are integrated into global supply chains, enabling efficient distribution worldwide. This global reach maximizes market presence and capitalizes on international demand. They offer important advantages for companies with a broader customer base.
4. Research and development (R&D) capacity. To drive innovation and maintain competitive advantage, it is key for large-scale operations to invest in R&D. The financial and resource capabilities of macro-factories often underpin the development and implementation of cutting-edge technologies.
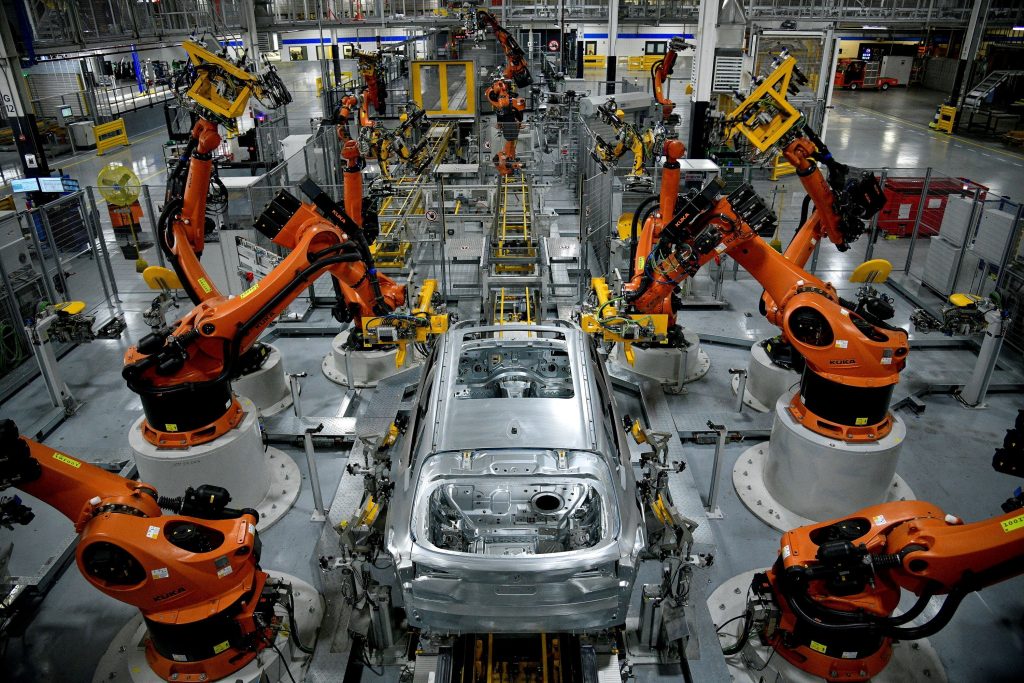
The role of digitalization and AI technology
BeChained’s example
Digitalization and AI are crucial for both micro-factories and macro-factories to optimize resources, enhance efficiency, and ensure sustainability.
BeChained built an autonomous AI solution, which exemplifies how technology revolutionizes manufacturing processes. This eliminates wasted energy, enhances uptime and efficiency through exception reporting.
1. Automating Repetitive Tasks. Digital systems and AI automate repetitive and time-consuming tasks. They free up human workers for more creative and complex activities. This not only improves productivity, but also enhances job satisfaction and innovation.
2. Upskilling Human Workers. By automating repetitive operations, upskilled workers stay focused on more strategic, value added and innovative tasks. This shift promotes continuous learning and adaptation. They are essential in a rapidly evolving manufacturing landscape.
3. Reducing Resource Use. AI-driven systems can optimize energy consumption and material usage, significantly reducing waste and operational costs. By monitoring and adjusting processes in real time, these systems ensure that resources are used as efficiently as possible.
4. Forecasting Downtime and Exceptions. AI technology forecasts predictive maintenance for equipment downtime, identifies exceptions, and optimizes Overall Equipment Effectiveness (OEE). This capability allows for proactive maintenance, reducing unexpected breakdowns and improving reliability.
5. Enhancing Predictive Capacity and Throughput. Turning data into actionable insights, AI systems enhance predictive capacity and throughput. By analyzing historical information and real-time data, these systems predict trends, optimizes production schedules, and improves manufacturing performance.
Conclusion
The future of manufacturing lies in leveraging the strengths of both micro-factories and macro-factories. This is supported by advanced digitalization and AI technologies.
Micro-factories offer localized, efficient, and customizable production, while macro-factories provide scale, automation, and global integration.
The integration of AI and digitalization is key. Solution, like BeChained’s, enhances resource efficiency, predictive maintenance, and operational excellence. Both models thrive in the Industry 4.0 landscape. Manufacturing continuously evolves. So, businesses should strategically assess and deploy those technologies and models, which best align with their strategic goals and business demands for a more future competitiveness.